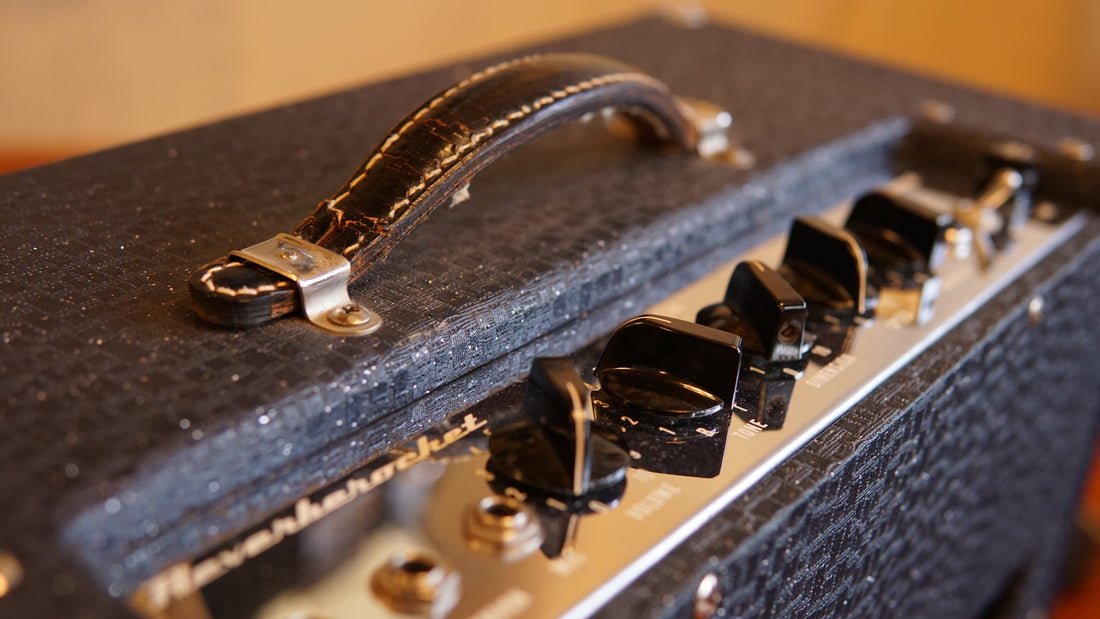
The Insider’s Guide to… Tube Amp Maintenance
Share
Our recently-launched podcast, The Truth About Vintage Amps with Skip Simmons, may just be one of the most informative (and entertaining) projects we’ve ever done. Every two weeks, vintage amp expert Skip Simmons drops some serious knowledge on us, answering a wide array of amplification questions from listeners around the world. It helps that he’s also hilarious.
In our first few episodes, we’ve learned what it’s like to be a drawbridge operator (that was Skip’s old day job), how to audition a potential amp repairperson and learned why Skip doesn’t put a three-prong cords on every old amp that comes through his shop. And, while a lot of Skip’s repair recommendations require an expertise in vintage gear, he’s also provided us with more than a few simple life hacks that nearly any amp owner can do.
With that in mind, here are a few of our favorite Skip tips… no soldering required.
Tube Amp Maintenance Anyone Can Do
Skip’s favorite piece of advice to nearly anyone with a noisy tube amp: Pull the tubes in and out of their sockets a few times. On decades’ old vintage amps, the sockets may simply be dirty.
If you want to go even further, Skip recommends putting a thin film on the tube pins. His lubricant of choice? Good old WD-40. He’ll spray it into an old jar and dip his finger into it. “I [then] wipe a thin film of it on the pins of the tube, put it back in the socket and pull it up and down four or five times. If it doesn't feel smooth – if it still feels like an old nail on a piece of wood – maybe I’ll add another thin film on the pins.”
Why WD-40 over amp and electronics specific cleaners like DeoxIt? “It has a solvent andit has a lubricant,” Skip answers. “If you spray it in an amp, you're screwing up, but if you apply it (lightly) to the pins, you are breaking down that [vintage amp] corrosion and leaving behind a little film of oil.”
Long-term Amp Storage
Need to store an amp that you seldom play or you’re about take a long trip? “Maintain [the amps] in storage the best you can,” Skip says. “If they have to be in the garage, I’d wrap them up in an old blanket or something. But if they’re in the house and they stay dry, and you don't have a crazy temperature range, it’s going to be fine. The key to it is what you do when you get back. First thing you should do is pull all the tubes in and out of their sockets, clean the tube sockets (see above). The second thing you should do, if you can, is fire that baby up with a Variac where you can turn it on over the course of 10 or 20 minutes. That’s what old amps really like when they've been sitting.”
Speaker Tears: 101
If you’re amp has an original speaker – or you just liked the sound of it – don’t throw it out.
“You can fix a tear or even a small hole in a speaker yourself, good as new,” Skip says. “Over the years, there has been all this stuff that they make to fix tears in speakers… and then there’s all this other stuff that people would use like nail polish and rubber cement. There are also actual products that were made since the ‘40s and ‘50s called speaker cement.” Skip doesn’t like any of the above. “What you really need is rubber-to-metal cement like they use on weather stripping, because when it dries its flexible. You don’t want that tear in your old speaker to be stiff, that’s going to mess with the sound.
“There’s commonly available stuff: One’s called Pliobond and the other is called Barge. They have it over at regular old hardware stores. You just put a little tiny amount over on the tear, it’s a permanent and works perfect. I've had quite a few people want to re-cone a speaker, a valuable speaker, just because it had a tear in it. No, no, no… fix it first. And don't use speaker cement because that stuff's junk, use the Pliobond or Barge.”
Skip suggests squeezing out the tube onto a flat surface and using the tip of a screwdriver to apply the cement to the speaker. “You just want to ease it down there. It just needs to be just enough to seal the crack. If you get the small tube and you're skilled you can actually squeeze it out of that small tube and just kind of work it right down where the tear is.”
Making a Modern Circuit Board Amp Better
Skip gets numerous requests to modify Fenders and other modern amps that have a printed circuit board in lieu of point-to-point wiring. Typically, it doesn’t make much sense. The only real modification he suggests for touring and gigging musicians is getting the jack replaced. “All they really need to give you some long lasting durability is to have that jack replaced with a real jack,” he says. Typically, these amps have flimsy plastic jacks that – if broken – could cause a ton of headaches.
He also adds that modern amps like a Fender Blues Junior run their tubes harder than their predecessors. Power tubes that typically can last decades may only last a year or two with some modern amps. (Skip likes the Sovtek 5881 for modern amps.)
Taking It Further: Learning How to Fix Amps
“I would suggest buying a classic, simple, easy to work on amp like a Silverface Champ. Learn how that works,” Skip says to any aspiring amp technicians. “Buy some broken ones and see what you can do. Hone up on your soldering skills, you're going to need a good volt meter and a Variac and some time. Start looking at [the amp], figure it out. Don't buy all the new books.” When it comes to reading materials, Skip has a clear favorite: Jack Darr’s Electric Guitar Amplifier Handbook.
“If you buy a new piece of test equipment – volt meter, capacitor meter, tube tester, whatever – everybody thinks that with that they can fix something. When you get a new piece of test equipment the only thing you should be doing with it at first is trying it on stuff that you know works! If you've got a new volt meter and you want to see if it works, look at an amp that works and compare the voltages you're getting to the schematics.”
Skip adds the following to all amp repair people eyeballing their next vintage project: “You don't want to redesign it, you just want to figure out what's wrong with it. The thing was made right at the beginning. Your job is to just make it right like it was at the beginning.”
We’ll add more Skip tips as we hear them… otherwise, do yourself a favor and check out the Truth About Vintage Amps with Skip Simmons. We think you’ll love it.